The Essential Elevator Maintenance Checklist
Elevator maintenance is critical for ensuring safety, reliability, and longevity of service in buildings. We’ve seen firsthand the difference that a rigorous and comprehensive maintenance checklist can make. Elevators thrive when they get the TLC they deserve. Keeping them running smoothly is all about giving them regular check-ups and fine-tuning. So, if you’re in charge of keeping a building running smoothly or if your job is to make sure everything facility-wise is up to snuff, we’ve got just the thing for you. Here’s a down-to-earth guide full of practical steps to prevent elevator breakdowns and make those lifts last longer than ever. Keeping elevators running smoothly and safely is at the top of our list. By sticking to a schedule of preventative maintenance, we’re not just fixing problems before they happen; we’re making sure these lifts do their job better and last longer than you’d expect.
Daily Inspections
- Visual Checks: Inspect the elevator car, doors, and buttons daily for any signs of damage or vandalism.
- Operational Tests: Perform basic operational tests, including door opening and closing, smooth ride, and accurate stopping at floors.
Weekly Tasks
- Emergency Systems Check: Test emergency lights, alarms, and communication systems weekly to ensure they function correctly.
- Door Mechanism: Inspect door panels, rollers, and tracks for wear and tear and clean any debris that could impede operation.
Monthly Inspections
- Safety Circuit Evaluation: Verify all safety circuits, including door interlocks and safety edges, are operational.
- Machine Room: Check the machine room for any signs of leaks, unusual noises, or overheating equipment.
Quarterly Maintenance
- Cable Inspection: Examine hoist ropes for fraying, stretching, or other damage. Consider tension and lubrication as part of this inspection.
- Pulley Systems and Counterweights: Inspect pulleys, sheaves, and counterweights for proper alignment and wear.
Biannual Checks
- Hydraulic System: Inspect the hydraulic fluid levels for hydraulic elevators, look for leaks, and test the system pressure.
- Brake System: Check the elevator’s brake system, ensuring brakes engage smoothly and effectively.
Annual Review
- Full System Inspection: Conduct a comprehensive inspection of all mechanical and electrical components, adhering to local safety regulations and standards.
- Load Test: Perform a load test to evaluate the elevator’s capacity and operational performance under stress.
Integrating AuditMate for Efficient Elevator Maintenance
Maintaining an elevator system’s optimal performance and safety is a complex task that requires meticulous attention to detail. In this scenario, AuditMate really steps up to the plate, making the whole maintenance routine a breeze. With AuditMate, a SaaS-based elevator audit software at their fingertips, building owners and facilities managers now have the power to streamline maintenance schedules with ease. This data-driven tool not only keeps elevators running smoothly but also ensures they meet all safety standards and performance expectations. Through AuditMate, the complexity of vendor management is simplified, offering a transparent, efficient pathway to monitor and enforce maintenance contracts. With AuditMate in their toolkit, people can make sure their elevators do more than just hit the markâthey soar beyond safety and performance expectations. This really ramps up how dependable those rides between floors can be.
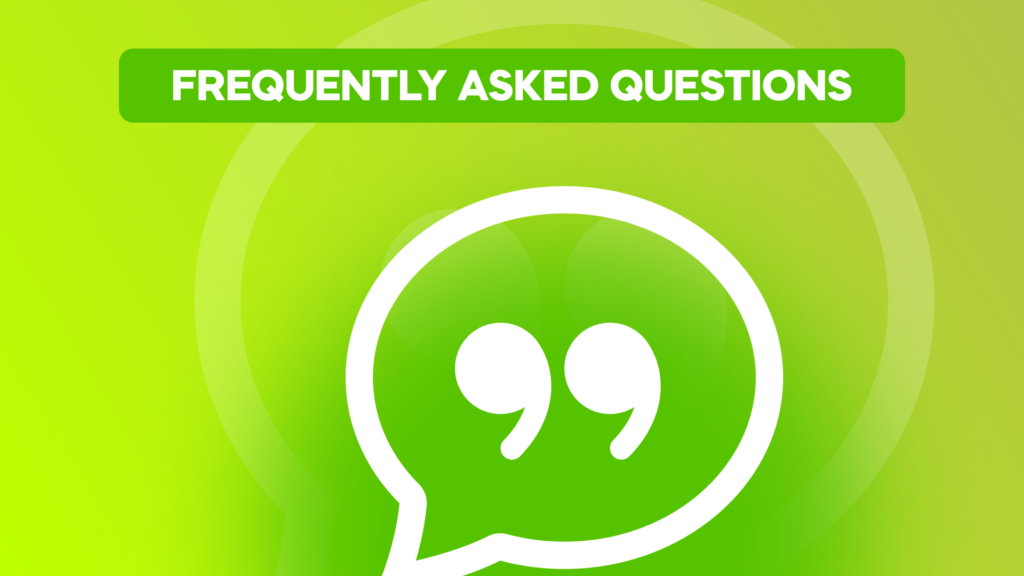
Frequently Asked Questions | AuditMate
FAQs:
How often should elevator maintenance be performed?
Elevator maintenance schedules vary based on usage, equipment type, and age. Depending on these factors, your elevator will need either monthly or quarterly maintenance. The key to this is the scope of work that needs to be completed in these visits. The proper scope of work, durations, and frequency will determine the reliability and life span of the elevator.
What are the signs that an elevator needs maintenance?
Indicators include unusual noises, slower operation, erratic stops or starts, and doors not opening or closing correctly, entrapments and shutdowns.
Can building staff perform elevator maintenance?
While daily visual inspections can be done by building staff, technical maintenance should always be performed by certified professionals.
How does AuditMate enhance elevator maintenance?
AuditMate brings everything you need into one place, making it a breeze to keep an eye on maintenance schedules, stay on top of compliance paperwork, and check how well your vendors are doing. This way, staying ahead with proactive maintenance management is as easy as pie.
What happens if elevator maintenance is neglected?
Neglecting elevator maintenance can lead to increased safety risks, higher repair costs, reduced equipment life span, and, in severe cases, elevator shutdown by regulatory authorities.